A Comprehensive Overview to Applying Foam Control Solutions in Your Workflow
Effective foam control is a critical facet of operational effectiveness that often goes forgotten. Comprehending the complexities of foam generation can substantially impact both efficiency and product top quality. This guide lays out the various difficulties posed by foam and the diverse options offered, offering a framework for selecting and carrying out one of the most ideal strategies. By examining crucial factors such as application compatibility and workers training, companies can optimize their foam monitoring initiatives. As we discover these parts, the potential for transformative enhancements in your operations ends up being obvious. What actions will you take next?
Understanding Foam Challenges
Foam challenges are a significant concern across various markets, impacting operational effectiveness and item high quality. The development of extreme foam can prevent procedures such as mixing, transport, and storage space, causing raised downtime and waste. In fields like food and drink, drugs, and petrochemicals, foam can interfere with manufacturing lines, creating item inconsistencies and contamination dangers.
In addition, foam can obstruct devices capability, resulting in expensive repair work and maintenance. In wastewater treatment, foam can interfere with clarifier procedures, resulting in reduced therapy effectiveness and governing compliance problems.
Understanding the underlying reasons for foam generation is vital for reliable administration. Aspects such as surfactants, temperature level variations, and frustration levels can all add to foam production. Recognizing these components permits industries to apply targeted strategies that lessen foam development while preserving product honesty.
Sorts Of Foam Control Solutions
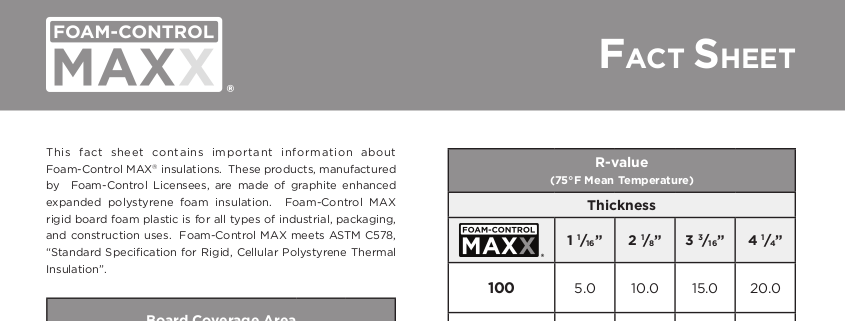
Mechanical solutions entail the usage of gadgets such as foam skimmers or defoamers. These tools literally get rid of foam from the surface area of fluids, thus preventing overflow and preserving optimal levels in reactors and tanks. Chemical remedies, on the various other hand, consist of the application of defoaming representatives-- substances that interfere with the foam structure, resulting in its collapse. These agents can be silicone-based, natural, or aqueous, each offering distinct advantages depending upon the application setting.
Finally, functional methods focus on procedure adjustments. This may include changing equipment specifications, such as temperature and stress, or transforming the flow prices of liquids to reduce foam generation. Executing good housekeeping methods can additionally minimize foam formation by minimizing impurities that add to foam stability.
Selecting the proper foam control service involves assessing the certain requirements of the procedure, consisting of the sort of procedure, the attributes of the materials involved, and safety and security factors to consider.
Choosing the Right Products
Choosing the best foam control products calls for a complete understanding of the certain application and its distinct obstacles. Aspects such as the type of foam, the atmosphere in which it takes place, and the wanted outcome all play essential roles in product selection. Foam Control. For circumstances, in markets such as food handling, it is necessary to choose food-grade defoamers that follow safety and security guidelines while successfully handling foam.
Additionally, consider the viscosity of the fluid where the foam trouble exists. Some items are created for low-viscosity applications, while others are customized for thicker liquids. Compatibility with existing procedures is one more crucial element; the picked foam control agents should integrate perfectly without interrupting total procedures.
Another critical factor is the method of application. Some products may need dilution, while others can be used straight. Assessing the ease of usage and the called for dosage can provide insights right into the item's effectiveness and cost-effectiveness.
Implementation Methods
Successful implementation techniques for foam control solutions need an organized technique that straightens product choice with functional demands. The initial step involves a complete evaluation of the procedures where foam happens, identifying specific areas that require intervention. By involving cross-functional groups, including manufacturing, design, and high quality assurance, organizations can gather understandings that educate the selection of the most reliable foam control products.
Next, it is essential to establish clear purposes for foam reduction, ensuring that these objectives are quantifiable and attainable. This might involve defining acceptable foam levels and the timelines for implementation. Educating employees on the homes and application methods of selected foam control representatives is equally important, as proper usage is important for optimal results.
In addition, incorporating foam control options right into existing workflows needs cautious planning. Organizations ought to establish a phased implementation strategy, enabling changes based upon preliminary results. Regular communication and comments loopholes with team involved in the procedure will certainly assist in prompt analytic and cultivate a culture of constant enhancement. Eventually, a well-structured method will certainly boost operational performance while efficiently handling foam-related difficulties.
Surveillance and Reviewing Efficiency
Monitoring and examining the effectiveness of foam control options is important for making certain that applied techniques generate the preferred outcomes. This process includes click here for more organized information collection and analysis to evaluate the performance of foam control representatives and strategies. Key performance signs (KPIs) must be established prior to implementation, enabling a clear standard against which to determine progression.
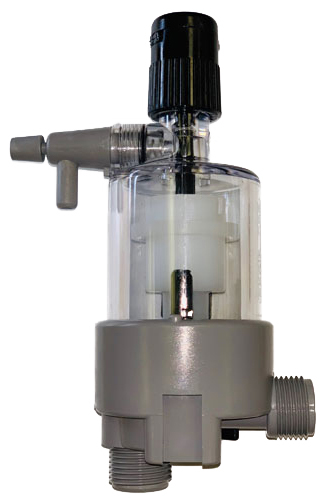
Evaluating effectiveness additionally needs periodic reviews of foam control treatments and agent efficacy. This can be accomplished via sampling and screening, permitting drivers to establish if present visit this page options are satisfying operational needs. Additionally, it is vital to obtain feedback from staff member that connect with these systems daily, as their understandings can disclose operational nuances that quantitative information may ignore.
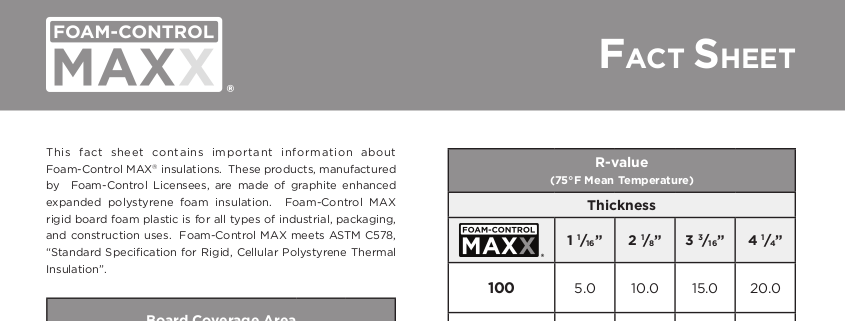
Inevitably, a structured monitoring and analysis framework assists determine necessary adjustments, ensuring that foam control services remain efficient, cost-effective, and straightened with business objectives.
Conclusion
In verdict, efficient foam control services are crucial for optimizing operational efficiency and keeping product top quality. A thorough understanding of foam obstacles, integrated with the selection of proper products and implementation approaches, promotes the effective management of foam generation.
Applying good housekeeping practices can additionally alleviate foam formation by reducing pollutants that add to foam security.
Selecting the right foam control items needs a complete understanding of the details application and its unique obstacles (Foam Control).Effective implementation strategies for foam control options need an organized technique that straightens product choice with operational requirements.In final thought, efficient foam control solutions are important for maximizing functional performance and preserving Discover More product high quality. An extensive understanding of foam difficulties, integrated with the choice of appropriate products and execution techniques, helps with the successful monitoring of foam generation
Comments on “Recognizing the Relevance of Foam Control in Food and Drink Processing”